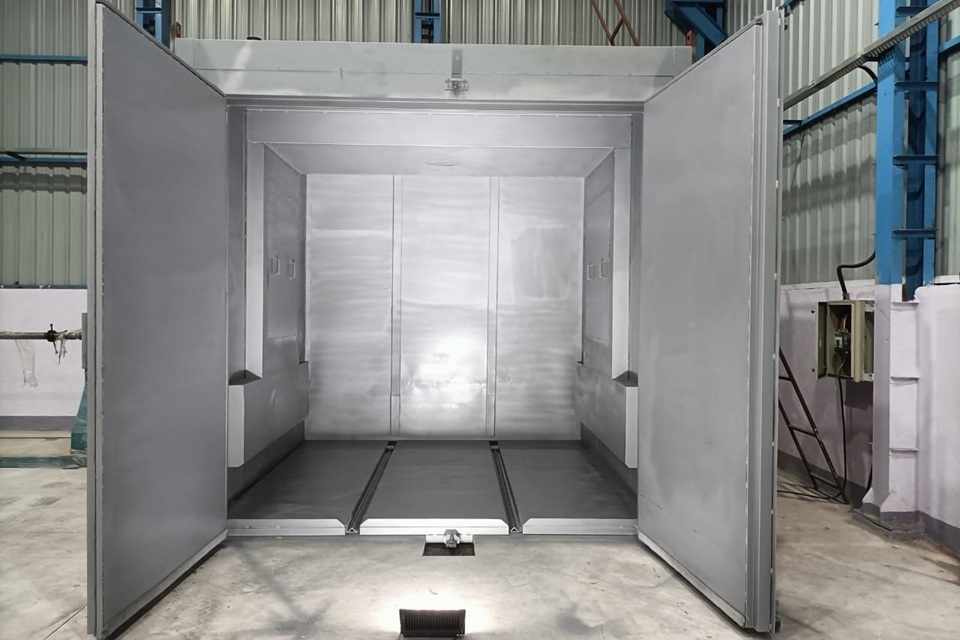
How Walk-In Powder Coating Ovens Improve Efficiency In Industrial Coating
- Business
- 8 March 2025
Efficiency is everything in industrial coating. Whether it’s automotive parts, metal furniture, or heavy machinery, every step of the process impacts production speed and overall costs. Walk-in powder coating ovens have transformed the way manufacturers handle large-scale coating, making it faster, more consistent, and cost-effective. These ovens streamline workflow, reduce energy consumption, and eliminate unnecessary delays, giving industries a smarter way to coat and cure metal parts.
Allowing Larger & Bulkier Parts To Be Coated & Cured In A Single Cycle
Traditional powder coating ovens often limit production due to size constraints, requiring businesses to coat and cure parts in multiple batches. Walk-in powder coating ovens solve this issue by accommodating oversized components in one go. This means manufacturers can coat entire frames, panels, or machinery parts without breaking them down into smaller sections, reducing the risk of inconsistencies. The ability to cure larger items in a single cycle improves uniformity and ensures a flawless finish.
In industries where large metal structures are common, such as aerospace and heavy equipment manufacturing, having an oven that can handle oversized parts is a game-changer. It eliminates unnecessary handling, reducing the risk of damage and contamination between coating stages. By streamlining the process, companies improve efficiency while maintaining the durability and quality of their finished products.
Reducing Production Time By Eliminating The Need For Multiple Small Batch Runs
Manufacturers know that time is money, and splitting production into smaller batches leads to inefficiencies. Walk-in powder coating ovens cut down on production time by allowing operators to process more parts at once instead of running multiple cycles. This eliminates delays caused by repeated preheating and curing phases, ultimately increasing throughput without compromising quality.
By reducing the number of cycles needed for large-scale coating jobs, businesses save not only on energy but also on manpower. Fewer batch runs mean less waiting time, allowing coated products to move onto the next stage of production faster. Whether it’s high-volume manufacturing or custom fabrication, the ability to coat more parts in one session drastically improves workflow efficiency.
Making Loading & Unloading Faster With Easy-Access Walk-In Designs
A well-designed powder coating oven doesn’t just improve curing efficiency—it also makes loading and unloading more manageable. Walk-in models provide operators with easy access to the curing chamber, reducing the time spent positioning parts. This design is especially beneficial when working with heavy or oddly shaped components that require precise placement for even coating.
With a walk-in powder coating oven, workers don’t have to maneuver around tight spaces or struggle to fit large parts into a confined curing area. The spacious layout allows for seamless transitions from the coating booth to the oven, minimizing handling time. This not only speeds up the process but also reduces the likelihood of errors, ensuring that each part is coated and cured correctly on the first attempt.
Minimizing Energy Waste By Maintaining Steady Heat Throughout The Curing Process
One of the biggest challenges in industrial coating is maintaining consistent heat during the curing phase. Walk-in powder coating ovens are designed to retain heat efficiently, preventing fluctuations that can lead to uneven curing. Instead of constantly reheating after each small batch, these ovens maintain a steady temperature, optimizing energy use.
The ability to maintain uniform heat distribution results in a more reliable finish, reducing the chances of defects such as orange peel or uneven adhesion. By controlling temperature loss, businesses lower their operational costs while achieving high-quality results. Whether running small jobs or large-scale production, energy efficiency plays a major role in improving long-term profitability.
Offering Flexibility For Different Coating Applications Without Constant Reconfiguration
Manufacturers often work with different coatings, materials, and part sizes, requiring an oven that can adapt to various applications without excessive downtime. Walk-in powder coating ovens offer the flexibility to handle diverse projects without constant reconfiguration. Their spacious design allows operators to switch between different coatings or part sizes without needing extensive modifications.
This adaptability is especially valuable for custom fabricators and job shops that handle a variety of coating requirements. Instead of limiting production to specific part sizes, businesses can take on a wider range of projects with minimal setup changes. This level of flexibility not only boosts productivity but also expands service capabilities, making operations more competitive in the long run.
Cutting Down On Labor Costs By Streamlining The Entire Coating Workflow
Manual handling, multiple batch runs, and inefficient loading processes add up to higher labor costs. Walk-in powder coating ovens streamline the entire workflow by reducing unnecessary steps, allowing workers to focus on other critical tasks. With fewer handling requirements and faster cycle times, businesses can get more done with the same workforce.
By integrating walk-in ovens into their operations, manufacturers optimize labor efficiency while reducing strain on employees. The improved workflow also lowers the risk of rework, ensuring that coated parts meet quality standards on the first pass. With less wasted time and effort, businesses see a direct impact on profitability while maintaining a high standard of production.